Operationally safe performance amid intensive chemical processes
Our Belt solutions have high performance and extreme resistance to abrasive processes, as they are developed with high quality compounds that preserve your carcass from chemical attacks and corrosion. Our belts meet the most important national and international safety standards and are built with trimmed or coated edges to increase their useful life.
MAXBELT Solutions for the Fertilizer Industry
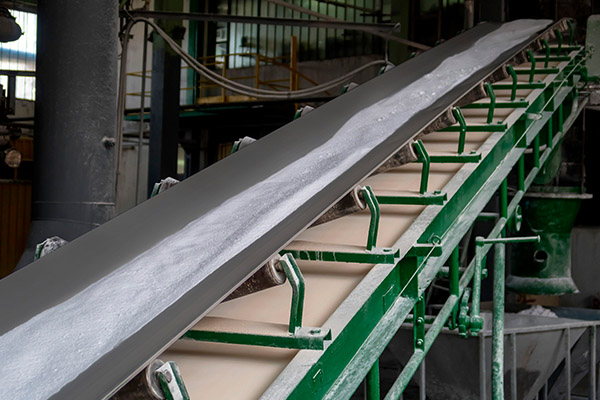
FOR®
Cover presenting the necessary qualities for the transportation of fertilizers, highly resistant to oils. It presents anti-static and self-extinguishing properties and withstands temperatures up to 248ºF. It meets ISO 340 (ASTM D 378-13.2 flame test standard/ MSHA 30CFR Part 18) and ISO 284 on electrical conductivity.
HD®
Compound developed to resist abrasion, cuts and bad weather, it is a great option for severe activities and for activities with rough edged or sharp materials, such as: iron ore, quartz, granite, limestone, basalt, gravel, manganese, petroleum coke, slag, etc. The HD® compound is recommended for materials reaching peak temperatures up to 194°F and complies with DIN W (0.00549 in³).
HD-MINERAÇÃO®
Cover specially developed to meet large mining companies and their strictest specifications. Product aimed at offering high resistance to impacts, cuts and abrasion, even facing heavy mining. With maximum abrasion loss of 0.00427 in³, it exceeds by more than 20% DIN W standard requirements. HD-MINERAÇÃO® is designed to operate with temperature peaks up to 194°F.
HDS®
Excellent performance compound designed to meet severe and high-impact operations, preventing tears. HDS® cover was developed to extend belt’s service life, thereby reducing the need for replacement. HDS® is recommended for materials reaching peak temperatures up to 194ºF with excellent abrasion resistance not exceeding 0.00305 in³ of maximum wear and tear.
HDS-EXTREME®
Cover designed for extremely severe and high impact applications, providing greater resistance to cuts and ripping and tearing. HDS-EXTREME® is recommended for materials reaching temperature spikes up to 176ºF and has extreme resistance to abrasion, not exceeding 0.00183 in³.
HDS-MINA®
Featuring all HDS cover advantages, such as maximum abrasion of 0.00305 in³, excellent performance on severe high impact applications and or high risk of tear; this cover combines anti-static and self-extinguishing flame properties in order to meet ISO 340 (ASTM D 378-13.2 flame test standard/ MSHA 30CFR Part 18) and ISO 284 on electrical conductivity, making HDS MINA® ideal for underground mines.
HOR®
Product developed to offer excellent resistance in the transportation of products with high presence of mineral and vegetable oils, urea and other elements with severe acidity conditions. Cover with good abrasion resistance and suitable for the transportation of materials with temperatures up to 248ºF, being recommended for metal parts bathed in oil, soybean meal, animal or vegetable fats, compost, fertilizers in general and insecticides.
LD®
Resistant and durable in highly abrasive applications; subject to cuts and to ripping and tearing, as well as in severe working conditions where HD® cover is not needed. It maintains good flexibility at low temperatures. Recommended for materials such as sand, gravel, coal, cement, phosphate, sulfur, salt, limestone, talc, cereal grains, wood, lime, etc. Suitable for materials reaching temperature peaks up to 176ºF. Abrasion level DIN X (0.00732 in³), and ARPM I.
LD-MINA®
Resistant and durable cover with good flexibility at low temperatures, designed to meet medium abrasion applications. It was designed for underground mining, in which anti-static and self-extinguishing properties are required. Recommended for materials reaching temperature peaks up to 176ºF. It meets the abrasion category level DIN X (0.00732 in³), ISO 340 (ASTM D 378-13.2 flame test standard/ MSHA 30CFR Part 18) and ISO 284 on electrical conductivity.
LD-REAÇÃO®
Cover developed for application in the fertilizer industry promoting greater resistance amid chemical reaction processes and chemical attacks. It also offers excellent abrasion resistance and can be used in processes up to 248°F.
RO®
Compound developed with moderate resistance in order to meet applications with oil (animal/vegetable) impregnation, slightly acids or basics. It is a great option for cotton seed transportation. This product is recommended for applications with temperatures up to 194ºF.
SH-EPDM®
The highlight of this cover is to be specially designed to offer maximum resistance to abrasive materials, as well as resistance to high temperatures, which can be applied in activities that reach up to 399.2°F. It is often used in the transportation of materials such as clinker, sinter, iron pellets, foundry sand, etc.
NOTE: For SH-EPDM® compound, the following minimum top cover thicknesses are recommended for maximum service life:
- Material temperature up to 320ºF – 1/4”
- Material temperature from 321.8ºF to 356ºF – 5/16”
- Material temperature from 357.8ºF to 399.2ºF – 3/8”
SHT®
Cover specially designed to avoid cracking or hardening that can be caused by thin and hot abrasive materials. This compound also has high heat resistance and can be applied to convey materials with temperatures up to 302ºF. It is ideal for products such as ashes, industrial carbon, petroleum coke, slag, foundry sand, clinker, cement and cast metals.
SHT-SUPER®
This cover presents the same qualities and characteristics as the model SHT®, that is, it was designed to offer greater heat resistance and to withstand temperatures up to 302ºF, without showing cracks or hardening during its application. Moreover, its composition allows a superior performance in relation to abrasion resistance.
NOTE: For SHT® and SHT-SUPER®compounds, the following minimum top cover thicknesses are recommended for maximum service life:
- Material temperature up to 194ºF – 3/16”
- Material temperature from 195.8ºF to 230ºF – 1/4”
- Material temperature from 231.8ºF to 266ºF – 5/16”
- Material temperature from 267.8ºF to 302ºF – 3/8”
Belt wear can vary greatly depending on the operational characteristics of each production or logistics process, such as: Contact our team and find the best solution for your operational profile.The best solutions come when we share our knowledge